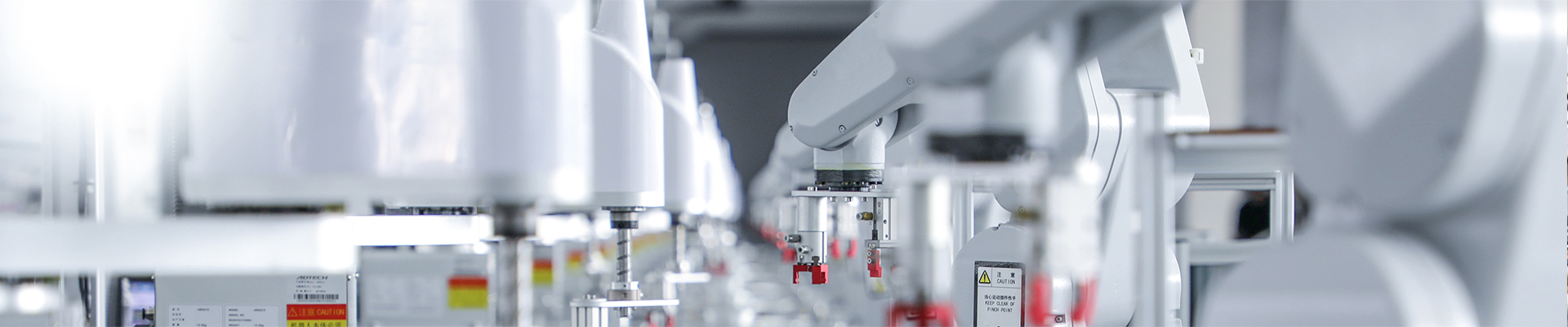
Several common problems and troubleshooting methods for raw burning in lime kilns
2023-11-23 16:50With the gradual implementation of national environmental protection policies, the amount of lime is also increasing year by year. As the main supplier of lime production line equipment, Henan Zhengkuang Machinery Co., Ltd. has summarized several common problems and failures in lime kiln raw burning based on years of customer maintenance experience. Approach.
NO.1 The particle size is too large
The calcining speed of limestone depends on the contact temperature between the lime content and the surface of the limestone. However, at a certain temperature, the calcining speed of limestone depends on the particle size of the limestone. The greater the material content, the slower the calcining speed. Here, since the thermal conductivity of lime is smaller than the progress of lime calcination, the thickness of the lime layer gradually increases, the harder it is for heat to enter the interior of the stone, and the calcination speed is also slower. Therefore, large pieces of limestone are often sandwiched, and burnt lime is the first reason for this. The particle size of ordinary vertical kilns should be controlled at 40-80mm. For large kilns, the particle size can be relaxed to 50-150mm. In order to save the cost of limestone, small stones can also be used exclusively.
NO.2 The fuel proportion is small or the fuel calorific value is low
The proportion of fuel used in a mixed-fired kiln is related to the technical performance of the kiln. The coal used in a mixed-fired kiln generally requires a calorific value of more than 5,500 kcal. The particle size must be controlled to a certain extent, and water must be added appropriately when using coal powder.
NO.3 The air supply is unreasonable
The stone in the lime kiln is heated and calcined by burning fuel, and the fuel is burned by oxygen (air). The combustion of any fuel must meet three conditions, including fuel, oxygen, and fire, all of which are indispensable, and the wind must be strong and the fire must be even. In addition to a certain proportion of fuel, it is also necessary to ensure the rationality of the air supply. On the cross section of the kiln, some areas have a large air volume and some have a small air volume. Areas with strong winds will be burned well, but areas with low winds will naturally cause raw burning. The air supply needs to be reasonable so that the air can be blown evenly across the entire kiln section so that the fuel can be burned evenly.
NO.4 Overheated
The quality of quicklime depends, first, on the content of calcium oxide and magnesium oxide, and second, on the rate of burning of quicklime. Raw burning means that part of the limestone is not completely decomposed, while over-burning means that the limestone is excessively calcined, making the quicklime dense, also called burnt lime or burnt lime. This part of quicklime has low activity and is difficult to be differentiated in subsequent production. The normal burning temperature of ordinary limestone is 1000-1200℃. Overburned ash usually results from burning at too high a temperature and for a long time. Cracks or glassy shells appear on the surface. The volume shrinks significantly, the color burns to black, and the block volume increases. To deal with over-burning, the first step is to consider whether the fuel ratio is too large, and it should be adjusted to a reasonable ratio. The coal quantity should fully consider the quality of the coal, and the air supply should also be adjusted to suit it.
Several operational problems and solutions
NO.1 The calcining area moves upward
In the calcining zone of an ordinary vertical kiln, if the top temperature rises in the middle of the kiln body, the ash temperature decreases, the CO₂ content decreases accordingly, the air volume is large, and excess oxygen increases, this means that the calcining belt has moved. After the calcining belt moves, the fuel will The upper part of the kiln burns early. When the charge falls to the calcining zone, the fuel has no firepower, and the amount of lime burned will naturally increase. The top temperature control is too high or the fuel entering the kiln is fragmented and burns prematurely. The wind pressure and air volume are too large, or the limestone particle size is too large, the ventilation is smooth, and the ash discharge amount is unbalanced, which is also the reason why the calcining area moves upward, resulting in large raw burning.
When encountering this situation you should:
01 When burning in a lime kiln, the wind pressure and air volume are reduced to move the fire layer downward. If the top pressure is low, the top pressure can be appropriately increased.
02 Increase the amount of ash discharge and increase the fuel ratio appropriately to supplement the heat loss caused by the high top temperature when it has not returned to normal, and adjust it to the normal value after it returns to normal.
03 Check and adjust the particle size of the raw fuel: If the fuel powder content is too high, add water appropriately to saturate it to increase its adhesion with the stone to delay the fuel burning time.
NO.2 The calcining area moves downward
When it is found that the top temperature is low and the ash temperature rises, the wind and fire have not burned out the fuel in severe cases. The burning of lime also increases, and at the same time the CO₂ concentration decreases, which means that the calcination zone moves downward. The main reason for this situation is that the air volume is small, the amount of stone loaded, and the amount of ash discharged are large, which makes the mixture move downward quickly, and the cooling zone is shortened. The air enters the calcining zone before it is sufficiently preheated, causing the calcium carbonate to decompose. As the CO₂ decreases, the amount of lime burned increases accordingly. In addition, if the raw materials are fragmented or the particle size deviation is large, the resistance in the kiln increases. At this time, the air pressure is not low, but the actual air volume is not enough.
When encountering this situation you should:
Appropriately reduce the amount of stone loading and ash unloading, appropriately increase the air volume, if the top pressure is too large, you can appropriately reduce the material batch, change the partial crushing of raw materials, appropriately increase the proportion of large particles, reduce the particle size difference, and reduce the resistance in the kiln. Small. Adjust the fuel and stone mass to meet the process requirements.
NO.3 The calcining area is extended
The extension of the calcining zone will cause the top temperature and ash temperature to be higher, CO₂ to decrease, and the amount of lime to be burnt will also increase. In severe cases, red ash will appear on the top of the kiln and under the fire, that is, red will appear at both ends. Nodules are formed in the kiln or local ventilation is poor. The reason is that the fuel ratio is too large and the uniformity of the limestone is poor. Nodules are formed in the kiln or local ventilation is poor. At the same time, there are nodules or materials hanging on the kiln wall, and ventilation segregation occurs. The nodules or hanging materials prevent the material from falling normally and the ventilation is poor. Since the lumps fall off under the impact of material flow, the calcining zone will also be extended for a certain period of time.
When encountering this situation you should:
Appropriately reduce production, adjust raw material particle size, reduce fuel ratio and increase air volume appropriately. Temporarily lower the height of the material layer and then return the material to the normal material level.
NO.4 Nodulation
Nodulation is a major fault in mixed-fired kilns, including gas-fired kilns. At this time, you can find:
(1) The ash temperature remains high all the time, raw burning occurs at the same time as the lime is unloaded, and the CO₂ content of the kiln gas remains low for a long time;
(2) The height of the material surface does not match the amount of ash discharged. The residence time of the material in the kiln is shortened, but the ash discharge time is extended. The ash is mixed with unburned fuel and uncalcined limestone to form green ash.
The main reasons are:
(1) The fuel ratio is too high, or there are too many impurities in the fuel, resulting in fusible matter.
(2) Although the ratio is not high, the fuel is locally concentrated and the calcination is intense to form kiln wall hanging materials.
(3) When there is a power outage or normal production cannot be performed for a long time, lumps may easily form when the high-temperature zone remains in the kiln for too long or impurities are present.
When encountering this situation you should:
01 Adjust the fuel ratio, adjust the wind pressure and reduce the impurity content of the raw fuel.
02 Reduce the loading amount or increase the ash unloading amount, lower the height of the material surface, expose the lumps or hanging materials, and make them fall off after cooling and loading impact. In severe cases, small blasting measures should be taken.
03 Change the mixing and distribution of raw materials and fuel to avoid excessive local fuel.
04 Increase the frequency of loading and unloading ash to increase the flow of materials and avoid sticking.
NO.5 partial kiln
When the kiln is in a partial kiln, it can be found from the top of the kiln that the material surface is tilted and the material is discharged quickly on one side. The fire layer on one side is dark, indicating that the temperature difference between the fire layer on the material surface is large. From the bottom of the kiln, it can be seen that ash comes out quickly locally or on one side when unloading ash, and red ash sometimes comes out when the ash temperature is high here. The main reasons are:
(1) The mixture is unevenly distributed or the ash is unevenly discharged, causing local nodules in the kiln, resulting in local ventilation segregation. Solving the fabric in this situation is critical.
(2) Improper adjustment of ash unloading equipment causes unbalanced ash unloading.
(3) The kiln shape structure is unreasonable, and the angle between the cooling section and the ash lowering section is too small, causing partial cornering and poor material discharge.
When encountering this situation you should:
Gas fired kiln FAQs
Except for the above common problems, the gas-fired kiln is roughly the same as the mixed-fired kiln. The key is the adjustment of the combustion flame temperature. Gas burning flames generally need to adjust the ratio of air and gas volume and pressure according to the composition and calorific value of different gases.
A common problem with high-calorific-value gas is overburning, while a common problem with low-calorific-value gas is overburning. However, specific analysis must be carried out when there is overburning or overburning. Many cases of burning when using high calorific value gas are caused by overburning. Due to the high calorific value of the gas, the flame forms a very high temperature as soon as it exits the burner, which causes the burner to sinter and blocks the flame from penetrating deeply. This will inevitably lead to raw burning in the center of the kiln. In other words, due to improper adjustment of the calcining temperature, the limestone will first be burned. The surface is sintered to form a hard shell. From the surface it looks like it is over-fired, but in fact it is raw inside. These problems are directly related to the kiln type and burner used.