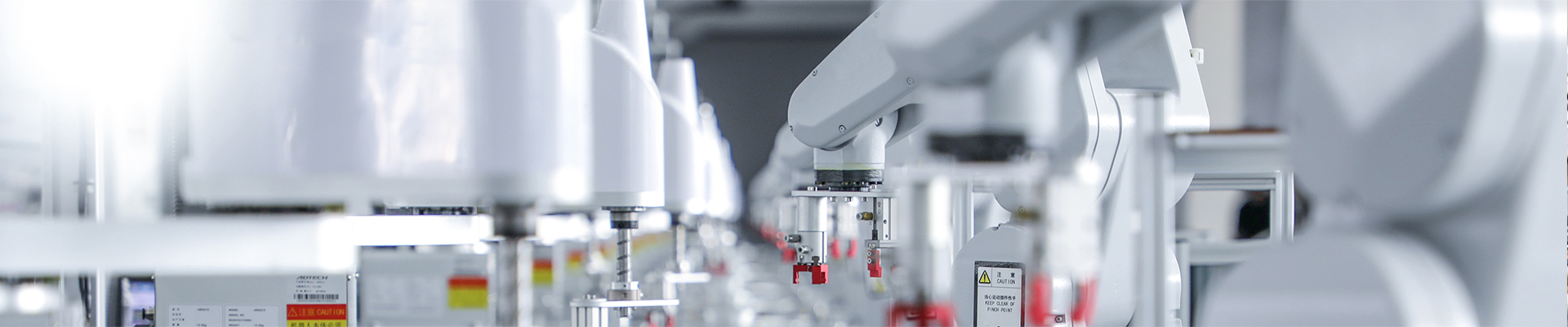
Aluminum Oxide Rotary Kiln
Alumina rotary kiln is a kind of metallurgical chemical kiln. It can also be used in metallurgical industry for magnetization roasting of lean iron ore in steel plant, oxidation roasting of chromium and nickelite, roasting of high metallurgical ore in refractory material plant and roasting of clinker in aluminum plant, alumina hydroxide, and roasting of chromium sand and chromium ore powder in chemical plant.
Alumina rotary kiln has strong structure, stable operation and high quality of products
Alumina rotary kiln is easier to operate than traditional equipment, reliable to use, compared with the same specifications of equipment, operation rate increased by 10%, output increased by 5%-10%, heat consumption reduced by 15%
- Information
Application: In many production industries such as building materials, metallurgy, chemical industry and environmental protection, rotary cylinder equipment is widely used for mechanical, physical or chemical treatment of solid materials.
Applicable materials: Mainly used in various heavy metals, copper, zinc, tin, nickel; Light metals, aluminum, magnesium, calcium, potassium, sodium, etc.
Metallurgical and chemical kilns are mainly used for magnetization roasting of lean iron ore in iron and steel plants in metallurgical industry. Oxidation roasting of chromium and nickelite; Refractory plant calcined high metallurgical ore and aluminum plant calcined clinker and aluminum hydroxide; Chemical plant roasting chromium ore and chromium ore powder and other minerals.
Luoyang Hanfei Power production of rotary kiln calcining system equipment through technological innovation, in the system adopts domestic and foreign hydraulic stop wheel device, the use of high precision metering piston pump, high precision speed control valve and contact graphite block sealing device and other domestic advanced technology. In order to improve the degree of automation, the kiln head uses industrial TV to watch the fire, the process simulates the fluorescent screen, and the calcination belt uses an infrared scanner to directly reflect the calcination situation of the calcination belt on the computer. The use of these new technologies is intuitive, easy to operate and reliable. The thermal system is stabilized, and the equipment operation rate is improved. Compared with the same specification equipment, the operation rate is increased by 10%, the output is increased by 5%-10%, and the heat consumption is reduced by 15%.
Structural features: the rotary kiln is composed of a cylinder, a supporting device, a sealing device, a feeding device and a kiln head combustion device, etc. The rotary kiln is a circular cylinder, which is inclined to be installed on several pairs of tugs. After the motor is slowed down, the cylinder is rotated by the pinion to drive the big gear.
Working principle: When the alumina rotary kiln is in normal operation, the main drive motor transmits power to the open gear device through the main reducer to drive the rotary kiln. The material enters the kiln from the end of the kiln (the high end of the cylinder) for calcination. Due to the tilt and slow rotation of the cylinder, the material both rolls in the circular direction and moves in the axial direction (from the high end to the low end), resulting in clinker cooling through the kiln head cover into the cooler. The fuel is injected into the kiln by the kiln head, and the exhaust gas generated by combustion is exchanged with the material and exported by the kiln tail.