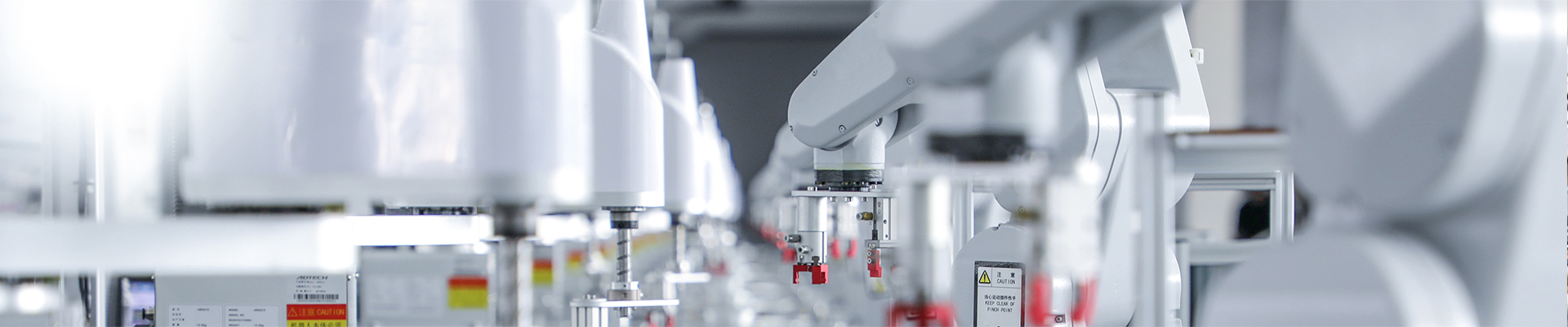
Calcium Aluminate Powder Rotary Kiln
The utility model discloses a rotary kiln for calcium aluminate powder, comprising a device body; The device body is composed of a base and a furnace body, the furnace body is located on the upper side of the base, the upper side of the base is provided with a storage platform, the storage platform and the base is provided with a shock absorber spring, the furnace body is provided with a feed box, the furnace body away from the feed box side is provided with a discharge box, the moving seal assembly is located on both sides of the furnace body, the furnace body is installed inside the scraper, and the scraper is both ends The dynamic seal assembly is connected, the furnace body is surrounded by a large gear, the large gear is sliding connected with the driving wheel, the driving wheel is located in the front end of the motor, the bottom end of the furnace body is provided with a supporting wheel shaft, the supporting wheel shaft is provided with a shaft seat. The utility model damping spring can buffer the potential energy generated when the internal material falls, which can effectively reduce the vibration of the device body and avoid the damage caused to the internal parts of the device body by large vibration amplitude.
- Information
The process of calcium aluminate rotary kiln is to make a mixture of aluminum hydroxide and calcium carbonate in a certain proportion, and then sintered at high temperature. Specifically, the required weight of aluminum hydroxide is first mixed with calcium carbonate in a certain proportion, and then the mixture powder is dried and removed for calcination. In the calcination process, it is necessary to preheat at a lower temperature first, and then gradually increase the temperature until the required heat treatment temperature is reached, and maintain for a period of time, so that the mixture is completely reacted to form calcium aluminate powder. The whole process needs to pay attention to adding an appropriate amount of flux to improve the sintering effect and reduce the heat treatment temperature.