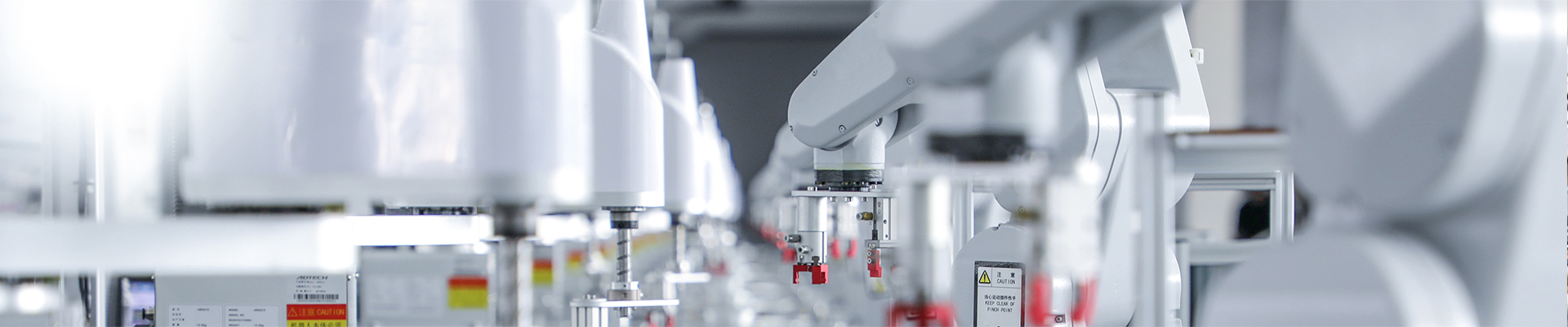
- Home
- >
- Products
- >
- Filter Machine
- >
Filter Machine
Technical features
1. Unique large diameter filtration structure, with a lightweight and reasonable design at the top of the filter disc. Compared with equivalent equipment at home and abroad, extremely
The earth has increased its production capacity and is currently the largest disc diameter in the world.
2. Unique design of distribution head device and central axis structure. Its structural approach greatly reduces filtration vacuum loss and increases
The filtration pressure difference has increased. And on the basis of similar foreign products, the vacuum channel has been increased, improving the unit area
The vacuum degree ensures a high flow rate of the filtrate, a dense filter cake, uniform thickness, and low moisture content. Adopting a single allocation header setup
The design has reduced the spatial area, making the layout of the factory more reasonable.
3. Adopting rolling bearings reduces the workload of equipment maintenance compared to domestic and foreign equipment, and avoids frequent replacement of wear-resistant materials
Grinding pads and other vulnerable parts reduce operating costs.
4. For the first time in China, the adjustment of the area of each filtration zone during equipment operation has been achieved, and the immersion rate has been adjusted by 38% to 53%
Whole.
5. The machine has no mechanical mixing device and adopts variable frequency speed regulation technology, which meets the requirements of different process conditions for product technology
Requirements for indicators.
6. The tank adopts open overflow, which makes unloading faster and overflow smoother. Completely eliminate material blockage and stacking
Accumulate.
7. The central angle of a single fan-shaped plate decreases, the disc diameter increases significantly, and the number of discs decreases. Due to the decrease in the central angle, it has expanded
The filtering and drying areas have increased production capacity. At the same time, replace the foreign product's filter plate with punched plate, and use special
The unique design and processing method have improved the stiffness and strength of the fan-shaped plate, making it sturdy and durable, and significantly increasing its
The porosity has increased the air permeability and filtration flow rate. And the weight of the single fan-shaped product is reduced, effectively reducing the burden on workers
Labor volume.
8. The top of the vertical fan-shaped plate can be replaced with a single piece of filter cloth through special design and processing methods, resulting in high labor intensity for workers
Large reduction, simple and fast operation, high degree of humanization. At the same time, there are few spare parts and components, and the equipment is running smoothly
This is greatly reduced.
9. Adopting the method of feeding both the middle and bottom simultaneously (or feeding from the bottom) avoids the precipitation and crystallization of the lower part of the vertical tray
Phenomenon. By using a fast pneumatic butterfly valve for material discharge, the equipment can be quickly discharged in the event of a malfunction, effectively preventing
Material precipitation.
10. Adopting a centralized lubrication station for dry oil makes lubrication more reliable, uniform, and sufficient.
11. Retaining the belt drive in the transmission system makes mechanical protection more reliable.
12. The pipeline connection between the distribution head and the vacuum receiving tank adopts a certain angle connection method to ensure smooth flow of the filtrate.
The connection between them is made of silicone rubber, which greatly reduces vibration and makes the movement more stable.
- Information
Equipment usage:
This series of products is mainly used for suspension filtration in the decomposition process of alumina plants, and can also be used for solid-liquid separation of various suspensions in other industries.
Working principle:
The working principle of the ZGF series vertical disc filter is to use the negative pressure formed by the vacuum pump to create a pressure difference on the surface of the filter disc. Under the action of the pressure difference, solid particles in the suspension are separated from water, and solid particles are formed on the filter cloth to form a filter cake. The filtrate is discharged through the filter cloth to achieve solid-liquid separation. The filter cake enters the drying zone, where most of the moisture is removed, and then enters the blow off zone. The compressed air generated by the blower blows off most of the filter cake on the filter disc, while the rest is discharged by a scraper. A complete cycle ends.