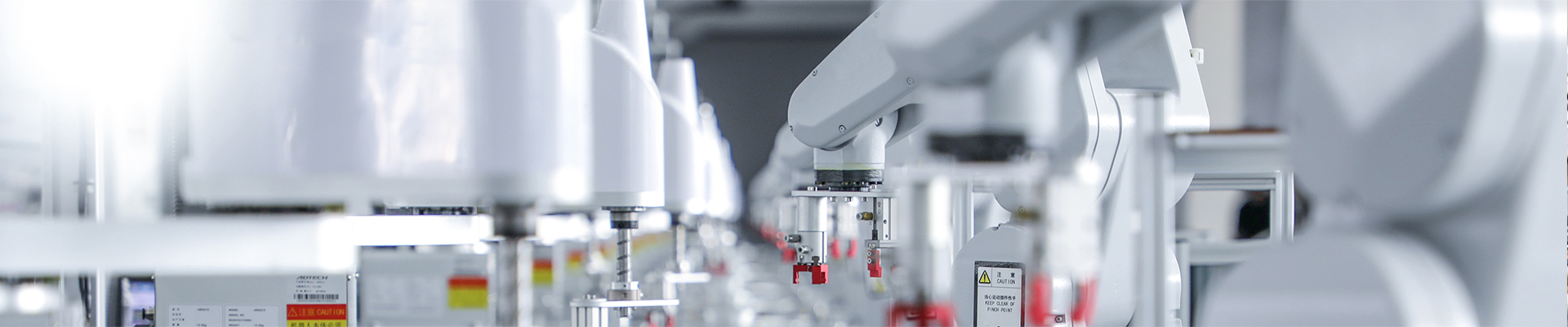
Ultra High Fine Grinding Machine
Ultra-high fine mill (600-1350 mesh) part of the fineness of 2500 mesh, high strength mill (high strength mill) in the main machine, the roller hanger tighten the inherent 1000-1500 kg pressure of the high pressure spring.
The ultra-high fine grinding machine is suitable for barite, calcite, potassium feldspar, talc, marble, limestone, dolomite, fluorite, lime, active clay, activated carbon, bentonite, kaolin, cement, phosphate rock, gypsum, glass, insulation materials and other Mohs hardness is not greater than 7. High fine powder processing of more than 300 kinds of materials in non-flammable and explosive mineral, chemical, construction and other industries with humidity below 6%. The finished product particle size can be adjusted freely within the range of 400-1350 (0.04-0.008) mesh, and some materials can reach up to 2500 mesh.
High strength mill. After the high strength mill starts to work, the mill roller rotates around the main shaft, and rolls closely to the grinding ring under the action of high pressure spring and centrifugal force. The pressure is 1.2 times higher than that of Raymond mill under the same dynamic conditions, so the output is greatly improved.
- Information
In order to further obtain fine powder with high mesh number, the downward wind generated by high-speed rotation of the analytical machine passes through the labyrinth of the cone structure, the air hole on the decompression ring enters the lower cavity, and then intersects with the upward wind that enters the lower cavity through the ventilation hole on the cone labyrinth plate, and then collides with the labyrinth pressure reducing plate of the cone structure to further classify under the action of blocking. The further refined differential returns to the upper chamber under the action of upward wind, and enters the cyclone collector into the finished product through the hollow chamber of the classifier and the aggregate chamber located above it. The excess wind pressure generated when the upper and lower wind converging is discharged from the exhaust hole on the installed filter screen through the air duct to play a secondary two-way circulation decompression effect.